Your shopping cart is currently empty.
What does THAT mean?
This will be the least technical "technical" page on the web. Our purpose is to explain, in laymen's terms, some of the issues relating to pressure, temperature, and flow that might be of interest to our visitors. Please tell us how we are doing.Basic Definitions
First, a few basic definitions that will set the stage for our technical discussion.Gravity
Newton tells us that two masses attract each other depending on how large they are and how close they are to each other. The attraction of the very large earth on everyday objects around us results in the weight of those objects, otherwise known as the force due to gravity. Almost everything that follows is based on this concept.Atmospheric Pressure
There is a thin layer of atmosphere surrounding the earth which is held in place by gravity. Although it is only 1/100 the diameter of the earth, this film increases in density as it approaches the surface of the earth. At the surface, the weight of the mixture of mostly nitrogen (78%) and oxygen (21%) that we call "air" creates a pressure on the surface of the earth that we measure at approximately 14.7 psia (pounds per square inch absolute). This pressure varies depending on your position and altitude and is reported by your local weather service in "Inches of Mercury" rather than psia. The barometer (a means of measuring atmospheric pressure) will be "29.95 and falling", for instance.Absolute pressure=the difference between a referenced pressure and the absence of pressure.
Gauge Pressure
Pressure gauges, and most other pressure measuring devices, generally measure gauge pressure rather than absolute pressure. In other words, a gauge not attached to any pressure source will show the "gauge" pressure as "0" even though, as stated above, the "absolute" pressure is actually 14.7 psia. In general, we are interested in the difference between the atmospheric pressure and what is in our compressor, so we want to know the "gauge pressure" of our tank or compressor.Gauge pressure=the difference between a referenced pressure and atmospheric pressure.
In PSI units it should be referred to as PSIg but the g is generally assumed and left off. By convention, measurements in psia always include the "a". As a rule, pressure gauges read gauge pressure.
Vacuum
If all this is true, what is a vacuum? A partial vacuum exists when a referenced pressure is below atmospheric pressure. Vacuum readings increase as the referenced pressure goes from atmospheric to absolute zero, or a full vacuum. A vacuum gauge at rest reads zero and increases until it could read -14.7 psig or -30 (29.92) inches of mercury if it were measuring a perfect vacuum. However, on earth, assuming an atmospheric pressure of 14.7 psia, a full vacuum can never be more than -14.7 psig or -30 inches of mercury, because that is all the atmospheric pressure there is here.Differential Pressure
For applications like filter monitors, we are also interested in differential pressures or the difference between two measured pressures. Differential pressure measurements are designated with the suffix -d so that in English units the pressure might be measured in PSId. One more definition:Differential pressure=the difference between two referenced pressures.
So gauge pressure is actually a sort of differential pressure where one of the referenced pressures is atmospheric pressure. Clear? I didn't think so..
Pressure Units
There are a huge number of pressure units theoretically possible. Any force over any area would be a pressure, so "Tons per Acre" would be valid but not very useful. There are only a limited number that are generally used. The Instrument Society of America as well as ISO have designated kPa as an international standard. The world has yet to be impressed, so different scales are used in different areas for different reasons. Here is a synopsis of the most prevalent:Additional conversion factors can be found here.
Pressure Gauges
A pressure gauge senses these pressures and displays what they are so a human can read them. Pressure gauges can be analog or digital or a combination of both. By far most prevalent type is the mechanical analog type that has been around for about 160 years. Around 1849, a Frenchman, Mr. Eugene Bourdon, invented the bourdon tube pressure gauge which is used for reading pressure ranges from 0-10 psi up to about 0-60000 psi and more. Instead of a long explanation of how a bourdon tube gauge works here, visit this page on the WIKA site for a good overview. Come back when you are done. Lower pressures, like 5 PSI down to 10 IWC (0.36 PSI) full scale, are generally read by diaphragm or capsule gauges. In all these types, the linear motion associated with changes in pressure is translated to the rotary motion of a pointer by the gauge movement.A pressure gauge is made up of the following parts:
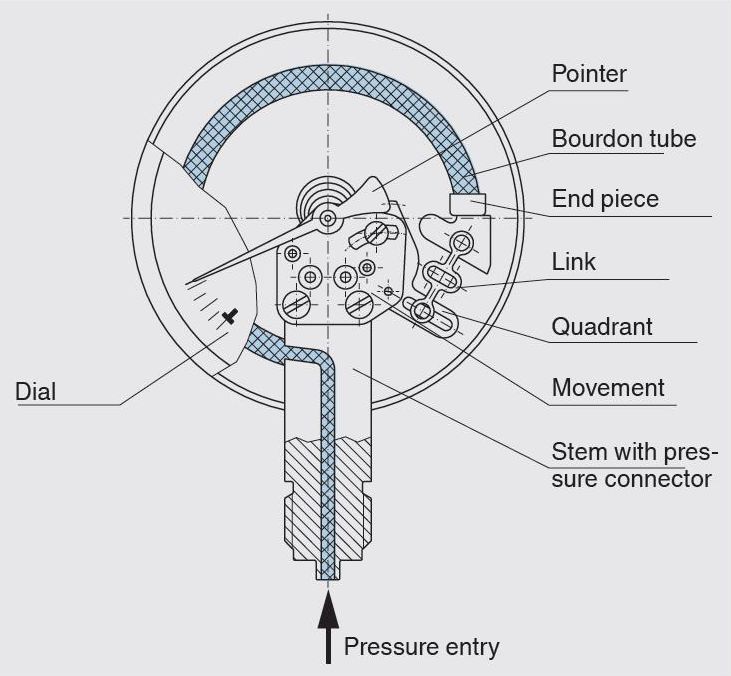
- The "pressure assembly". Usually soldered, brazed, or welded together and made up of:
- Socket - a bored out and threaded barstock piece that accepts the sensing element.
- Sensing Element - Bourdon Tube or Capsule.
- Tip - connected at the moving end; closes the Bourdon tube and provides for link.
- The "movement". Usually a rack and pinion geared assembly that translates the linear motion of the element into the rotary motion of the pointer. It consistes of:
- Link - a free moving piece that links the tip to the sector.
- Sector - a "rack" gear and fulcrum with a pivot point between the tip and the pinion.
- Pinion - a gear with center shaft that attaches to the pointer.
- Plates - hold the gears together, the dial on, and mounts to the socket.
- The "dial". Mounts to the plates and contains the pressure units and graduations.
- The "pointer". Points to the appropriate pressure. We hope.
- The "case". Holds and protects all the other parts in the assembly.
- The "lens". Acts as a clear cover so the operator can see the pointer and dial.